While innovation is often associated with technology and production, companies also need to carry through this approach into their health, safety and environmental performance.
This is the view of Ramesh Dhoorgapersadh, General Manager: Global Operational Excellence at Omnia group company BME. Born as a pioneer of cold emulsion technology in South Africa in 1984, mining solutions company BME also applies its innovative approach to support a safety culture across its supply chain, said Dhoorgapersadh.
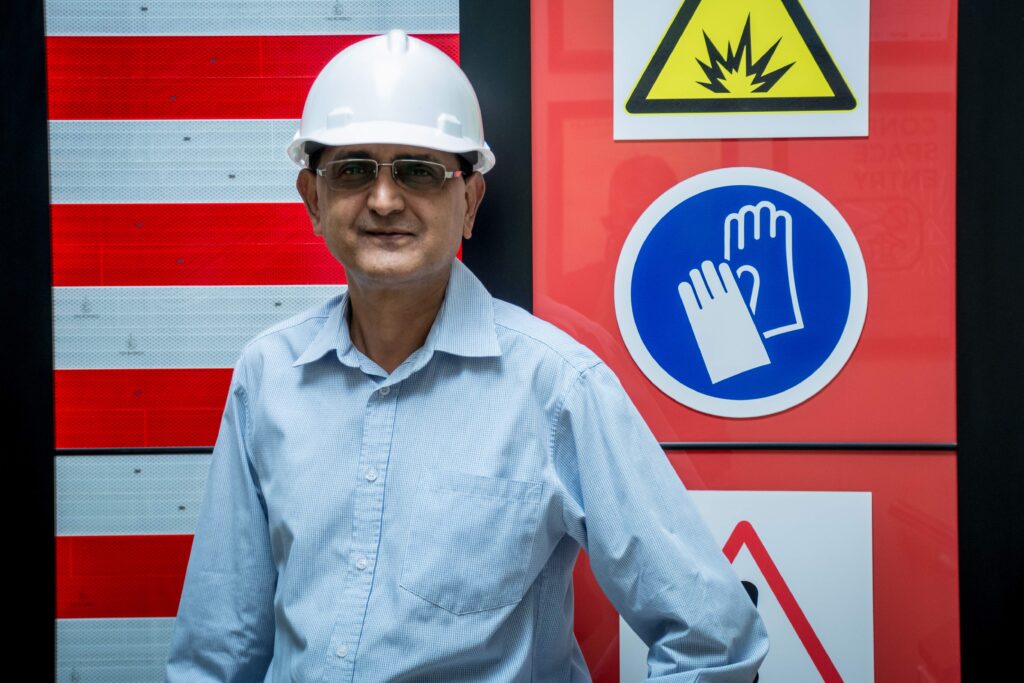
“Guided by Omnia’s commitments to people and planet, we build health, safety and care for the environment into every decision and at every stage in our value chain,” he explained. “This extends from the design and manufacture of our explosives, through the transportation and storage of product, to the on-site preparation and blasting.”
Zero harm
Dhoorgapersadh highlighted that this drive towards zero harm was also a critical consideration among mining customers, whose environmental, social and governance (ESG) performance also considered the safety and sustainability of their supply partners. Safety has in fact been at the core of BME’s operation through the intrinsic stability of its dual salt emulsion.
“Our emulsion is a class 5.1 oxidising agent which can be safely transported, and only becomes explosive when sensitised by a gassing agent in the blasthole,” he said. “Even the manufacture of BME’s INNOVEX™ emulsion is a safer process, as it does not need to be heated to high temperatures.”
Dr Rakhi Pathak, BME’s Senior Product Manager for AN Products, Equipment, and Services, noted that quality processes are integral to ensuring the development of safe products that are environmentally sustainable.
Chemistry
“The chemistry advantage of our dual salt emulsions over traditional single salt emulsions makes them highly stable and robust,” said Dr Pathak. “The addition of calcium nitrate to our oxidiser makes our technology unique and contributes greatly to our success.”
With a formulation that keeps the nitrates in solution, there is no phase separation even after long transportation distances and multiple stages of pumping. This means that emulsions manufactured at BME’s production plants can be safely transported to other countries and elsewhere with no risk of reduced performance.
R&D
Dr Pathak emphasised the careful consideration of risks not only in applications but in the product development process.
“We look at the features that the customer will need, to use each product efficiently and safely, and then engineer the product with those aspects in mind,” she explained. “This means understanding the level of skills of users on site, and supporting with the necessary training material as needed.”
Safety is therefore built into the research and development process – from ideation to commercialisation – in accordance with stringent quality management systems.
Used oil disposal
“There are specific stage-gates throughout the value chain to make sure that products conform to industry standards and the customer’s specifications,” she said. Among the innovations that have allowed BME’s emulsions to make such a positive environmental impact is its incorporation of used oil as a fuel agent. The company’s network of used oil collectors takes millions of litres of hazardous oil from customers and other sources, ensuring that it does not contaminate water or land.
The used oil initiative is also a powerful enabler for small businesses, promoting the sustainability of local economies by empowering entrepreneurs to contribute to environmental protection. This all adds to the value of our customers’ relationship with BME, by reducing their environmental compliance risk. In line with the Omnia sustainability vision, BME has also equipped many of its manufacturing facilities with solar energy to reduce its carbon footprint and ensure business continuity.
Blasting risk
Dhoorgapersadh noted that BME’s safety and quality systems are applied in all the countries in which the company operates, and in accordance with specific national regulations on explosives. This needs constant attention to detail, such as the growth of communities around operational sites.
“It is not uncommon for us to witness encroachment by communities around mining or quarrying sites,” he said. “Our risk assessments ensure that the blasting risk circles around a site are accomodated to ensure community safety.”
He said that safety, health and sustainability were corporate journeys that demanded continuous learning and improvement through innovation. This includes monitoring the results of BME’s initiatives – such as its Safety for Life brand – and constantly raising the bar.