For a long time, the dry beneficiation of quartz sands remained unclaimed. ERGA has developed and manufactured a highly inductive separator ERGA RollMag for effective dry beneficiation on the basis of many years’ experience of rare earth magnet production. We have conducted studies to prove the effectiveness of dry magnetic beneficiation. In this article you will learn the test results, methods and solutions offered by our equipment.
Quartz sand consists of SiO2 particles smaller than 2 mm. It is formed by the decay of igneous and metamorphic rocks containing large amounts of quartz (SiO2). Quartz sand contains impurities such as clay, feldspar, lime, iron oxide and carbonates.
The diagram shows the average distribution of iron oxide by mineral in silica sand deposits.
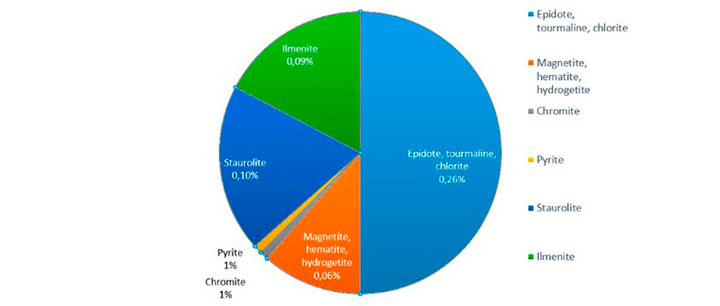
The diagram shows that to reduce iron oxide in silica sands it is advisable to use magnetic separation, due to the presence of weakly magnetic minerals – ilmenite, epidote, magnetite, hematite, etc. in the deposits.
Silica sand after beneficiation and removal of minerals including iron is used in various industries, including glass and chemicals. The content of clay and iron in quartz sand should be below a certain level, depending on its intended use.
THE PURPOSE OF RESEARCH
The goal of ERGA in this research was to make the product as reliable as possible in operation. As is known, deposits of quartz sand can be found in many countries around the world, and only in some places are there deposits of high purity. In our studies, we used samples from a North African deposit.
To achieve high purity in silica sand, it is necessary to remove the impurities present in the raw silica ore or silica sand. To effectively remove these inclusions, it is necessary to conduct a thorough physical, chemical and mineralogical analysis of the raw material. By selecting the appropriate settings for a dry magnetic separator depending on the composition of the raw material, silica sand can be beneficiated.
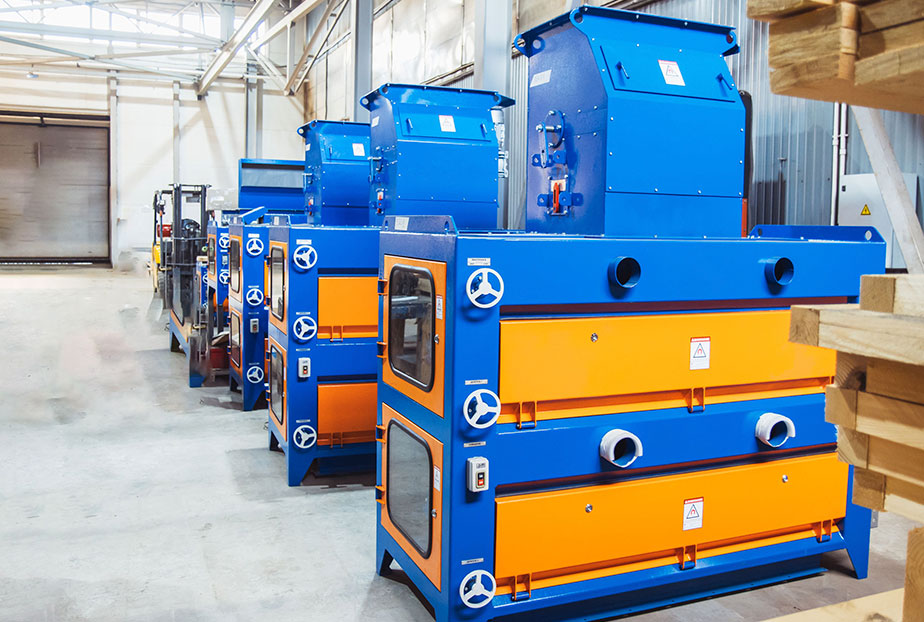
To achieve high purity in silica sand, it is necessary to remove the impurities present in the raw silica ore or silica sand. To effectively remove these inclusions, it is necessary to conduct a thorough physical, chemical and mineralogical analysis of the raw material. By selecting the appropriate settings for a dry magnetic separator depending on the composition of the raw material, silica sand can be beneficiated.
During our beneficiation research, a dry and physical magnetic separation method was used. The magnetic separation experiments used a model of the ERGA RollMag magnetic separator, known for its high field strength. Silica sand samples underwent a three-stage purification process consisting of low- and high-productivity stages.
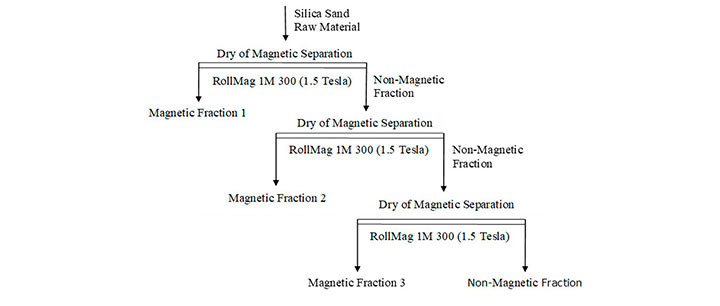
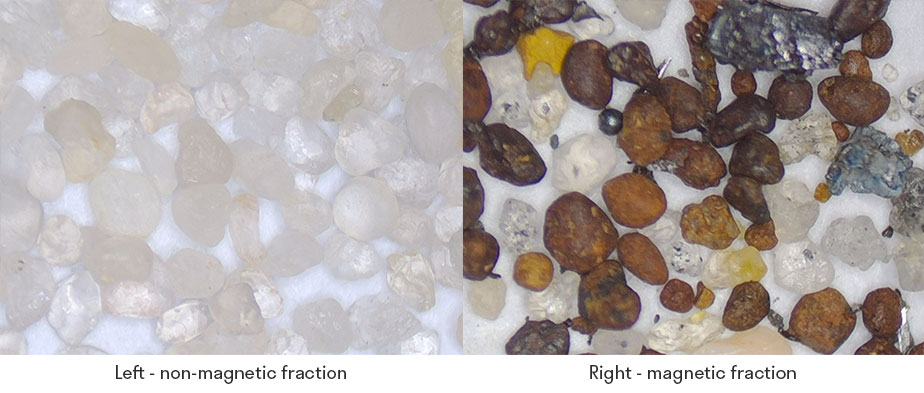
According to the chemical analysis, compared to the original sand, the content of iron oxide Fe2O3 decreased from 0.054% to 0.01%, the content of silicon oxide SiO2 increased from 99.80 to 99.98% also due to the reduction of titanium and aluminum oxide and the removal of aggregates.
The effectiveness of the ERGA RollMag magnetic field in extracting iron oxide minerals, as well as silica with iron oxide inclusions, is shown in the photo.
ERGA ROLLMAG OPERATION PRINCIPLE
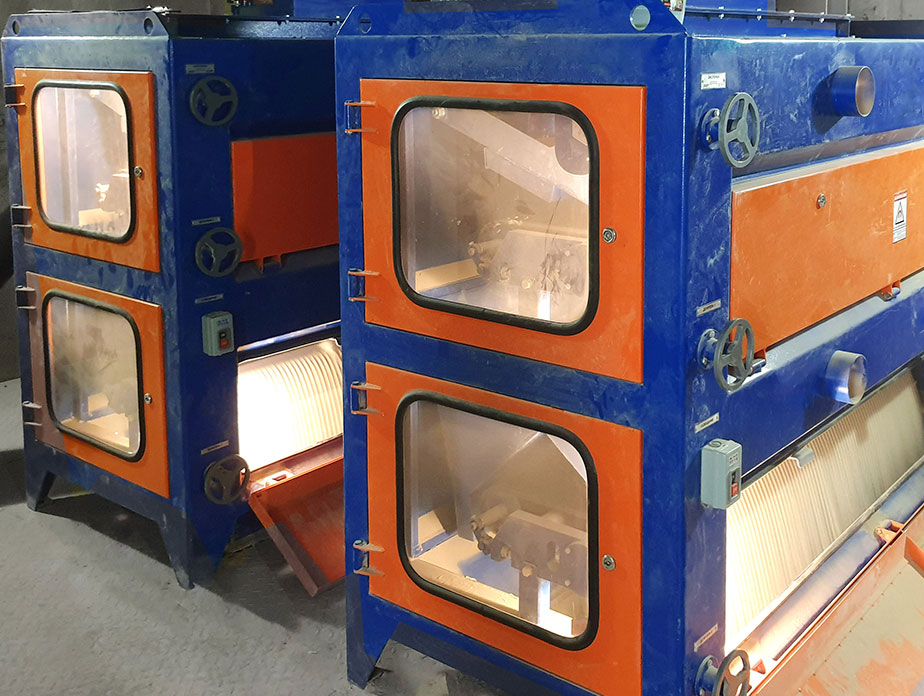
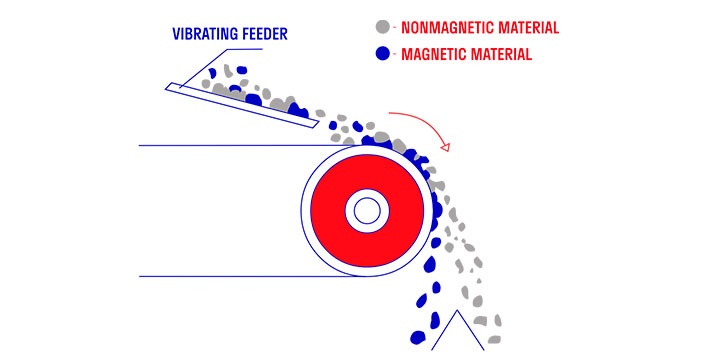
The RollMag operates based on the following principle: the material enters the vibrating feeder from the receiving hopper of the separator. It is then fed in a uniformly distributed flow to the belt conveyor, which is equipped with a magnetic drive shaft. The magnetically susceptible inclusions present in the enriched material stream are attracted to the shaft due to the magnetic field generated by the shaft. These inclusions are held on the surface of the Kevlar tape that envelops the shaft, and they are transported to the unloading zone. To separate the non-magnetic component of the material from the inclusions with low magnetic susceptibility, a divider plate is installed beneath the magnetic shaft. The inclusions with low magnetic susceptibility change their trajectory of movement under the influence of the powerful magnetic field. Prior to the main separation, the magnetic drum separator is installed. This solution protects the ERGA RollMag from damage caused by large metallic impurities.
In its research, ERGA has successfully used dry magnetic separation technology. The magnetic separator was customized individually and its characteristics were set taking into account the characteristics of the material itself and the magnetic properties of unwanted inclusions.
Our innovative magnetic separation equipment, new technological processes and quality control guarantee the almost complete absence of impurities, inclusions and foreign colors in the glass produced.
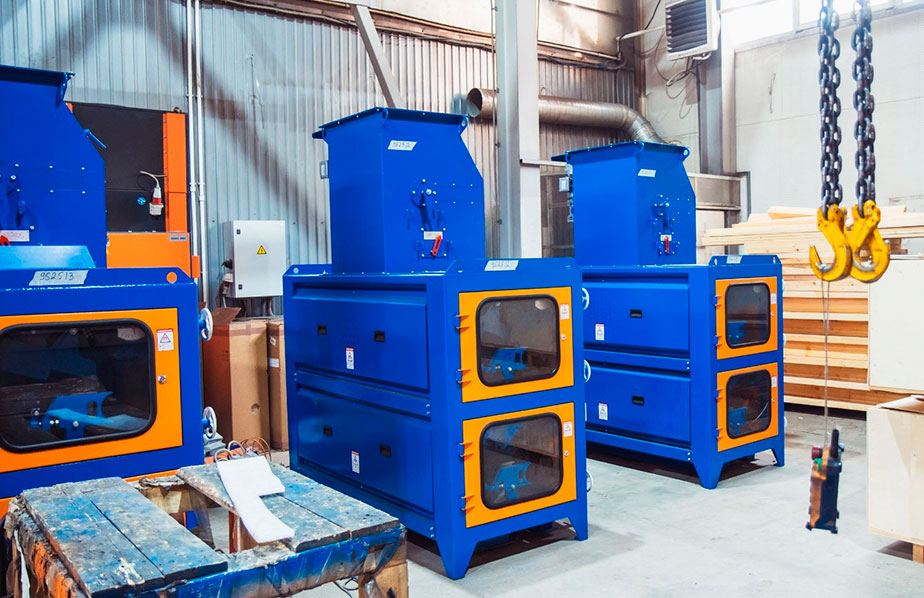
The characteristics and parameters of each magnetic separator are individually tailored to the specific application in order to maximize the effect of magnetic separation.
The advantages of the new magnetic roll separators:
- Achievement of a previously unavailable high degree of separation efficiency for feldspar, silica sand and other materials;
- Possibility of automated remote monitoring system REMOS which monitors equipment status, transmitting data in real time;
- Fully enclosed constructions with the aspiration option.
ERGA, with its robust research and development base, design bureau, and dedicated production line for permanent magnets, excels in solving the most complex tasks set by our customers. Our solutions are cost-efficient and sustainable, ensuring the highest quality and performance.
Get in touch with us and let’s talk about the solutions
you need:
- Website: www.ergaglobal.com
- Mail: info@ergaglobal.com
- Tel: (0232) 230 04 71
- LinkedIn: https://www.linkedin.com/company/ergaglobal
- Youtube: https://www.youtube.com/@erga-global
- Facebook: https://www.facebook.com/ergaglobal
- Whatsapp: https://api.whatsapp.com/send?phone=905425653742
- Telegram. https://t.me/ERGA_Global
About ERGA
ERGA is a global manufacturer of magnetic systems and industrial equipment. The key activity of the company is development and production of equipment for mineral processing, air and gravity separation, complete solutions for processing of various waste and separation of materials by electrical properties.
✓ +30 years of manufacturing experience
✓ ISO 9001: 2015 quality control system
✓ > 25 000 m² of modern production facilities
✓ Over 200 qualified employees
✓ Design and engineering solution of the tasks
✓ Full production cycle
✓ Professional service support
✓ In-house material research laboratory
Strategic management system is implemented in our company. Special attention is given to implementation of the programs, aimed to improve the processes of product quality control and arrangement of effective customer relationships.